On a sunny spring morning in Hanover, Germany, I’m heading to meet a robot.
I’ve been invited to check out the G1, a humanoid robot created by the Chinese tech company Unitree, showcased at Hannover Messe—one of the biggest industrial trade exhibitions worldwide.
The G1 stands about 130cm (roughly 4’3″) tall and is smaller and more budget-friendly compared to other humanoid robots. Its smooth, agile movements have caught attention online, with viral clips of it dancing and doing martial arts.
Today, Unitree’s sales manager, Pedro Zheng, is operating the G1 remotely. He explains that users must custom-program each G1 for autonomous actions.
As G1 moves around, it draws a crowd—unlike many of the other machines on display. People approach it, shake its hand, test its reactions with sudden movements, laugh at its gestures, and even apologize if they bump into it. Its human-like form—though slightly uncanny—makes it more approachable. Unitree is one of many companies globally racing to develop humanoid robots.
The potential is significant—businesses see the appeal in a tireless, salary-free workforce. In homes, such robots could one day become all-in-one helpers, taking care of chores like laundry and dishes.
However, the tech isn’t quite there yet. Industrial robots like robotic arms are common in controlled environments like factories and warehouses, where risks are minimized. Introducing humanoid robots into unpredictable places—such as homes or restaurants—is far more complex.
They must be both strong and safe. A poorly timed fall could be dangerous. The real hurdle is developing advanced artificial intelligence that can reliably manage these machines.
As a Unitree spokesperson told the BBC, AI hasn’t reached a true turning point. Current systems struggle with logical reasoning and completing complex tasks in a structured manner.
At this stage, G1 is mainly aimed at research labs and tech developers, with its open-source software enabling further advancement. For now, most businesses are focusing on industrial use cases, particularly in logistics and manufacturing.
Elon Musk is leading the charge with Tesla’s humanoid robot, Optimus. He recently announced plans to produce thousands this year, expecting them to handle useful tasks in Tesla’s factories.
Other automakers are exploring similar paths. BMW has introduced humanoid robots at a U.S. plant, and Hyundai has placed a large order with Boston Dynamics, which it acquired in 2021.
Thomas Andersson, founder of research firm STIQ, tracks 49 companies working on humanoid robots with both arms and legs—and over 100 if you include robots with arms that move on wheels.
Andersson believes Chinese companies are in a strong position to lead. With a vast supply chain and efficient R&D processes, China has a major advantage.
Unitree’s G1 reflects this edge—it’s relatively affordable at $16,000 (around £12,500). Investment trends also favor Asia. STIQ reports that nearly 60% of all funding for humanoid robotics goes to Asian countries, with the U.S. getting most of the remainder.
Chinese companies also benefit from strong government support. For instance, Shanghai hosts a state-funded robot training center, where humanoid robots are being trained to complete practical tasks.
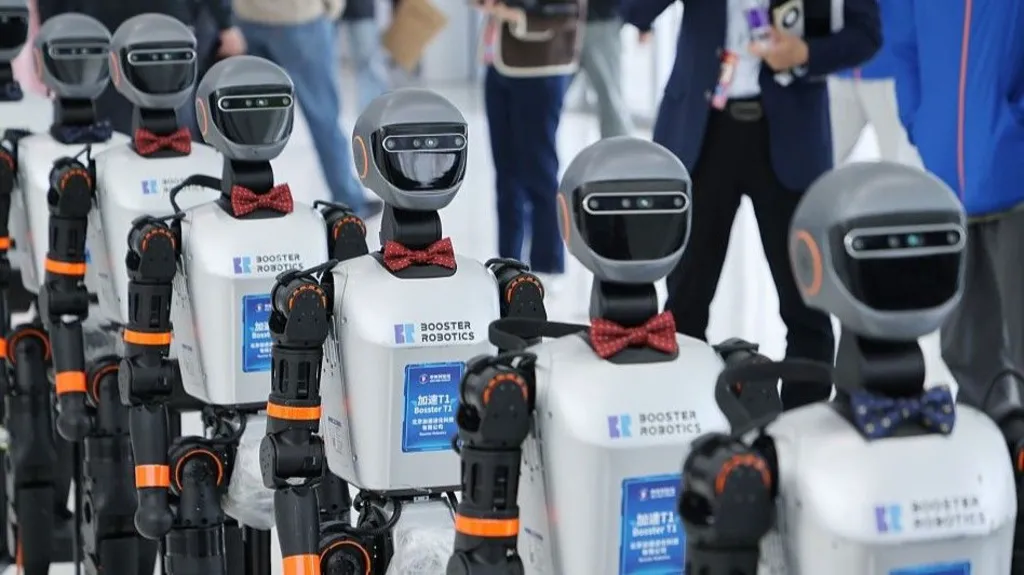
Chinese companies are in a strong position to lead the humanoid robot industry.
So how can American and European robot developers stay competitive?
Bren Pierce, a robotics entrepreneur from Bristol, England, has launched several robotics ventures. His latest company, Kinisi, recently introduced the KR1 robot.
Although the KR1 was engineered in the UK, it will be manufactured in Asia. According to Pierce, Western firms face a major challenge: they rely heavily on Chinese-made components.
“You end up sourcing motors, batteries, and resistors from China anyway,” he explains. “Shipping all those parts to the West just to assemble them makes little sense when you could build everything directly where the components are made—in Asia.”
To keep production costs down, Kinisi has opted not to pursue a full humanoid design. Aimed at warehouse and factory use, the KR1 doesn’t have legs.
“These environments already have flat flooring. Why add the cost and complexity of legs when a wheeled base is more practical?” Pierce asks.
Whenever possible, the KR1 uses standardized, mass-produced parts—like electric scooter wheels.
“Our approach is to use readily available components. Motors, batteries, processors, and cameras—we use commercial off-the-shelf parts,” he says.
Like Unitree, Pierce believes the key differentiator is the software that enables robots to collaborate effectively with humans.
“Many companies produce sophisticated robots, but they require advanced robotics knowledge to operate,” he notes. “We’re designing something that a typical warehouse or factory worker can learn to use in just a few hours.”
Pierce says the KR1 can learn to complete a task after a person guides it through the process 20 to 30 times.
Kinisi plans to release the KR1 to pilot customers for testing later this year.
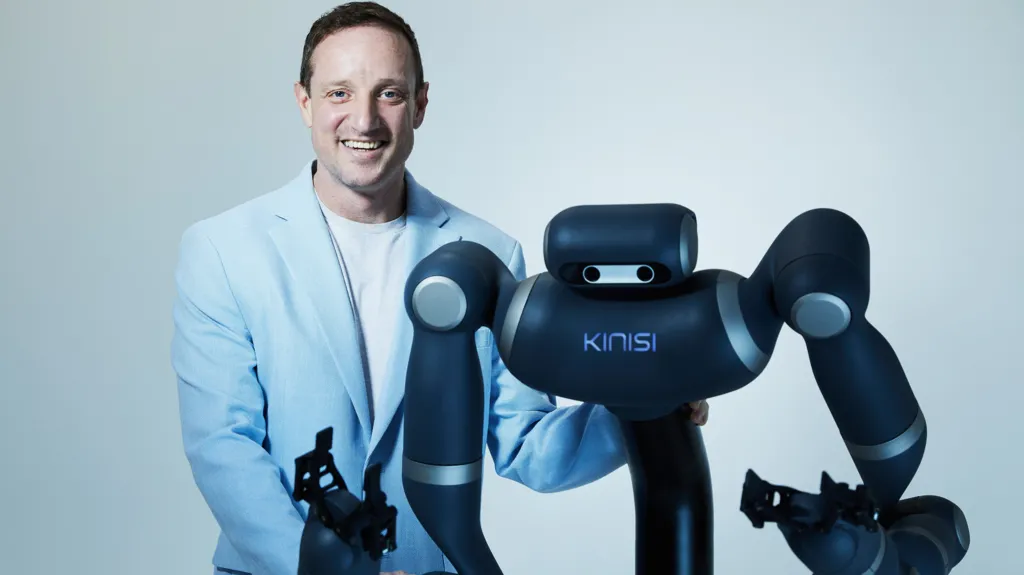
Bren Pierce says Kinisi’s robot is designed for quick and simple training.
So will robots eventually move from factories into everyday homes? Even the optimistic Bren Pierce admits that reality is still far off.
“For the past 20 years, my ultimate goal has been to build an all-purpose robot,” says Pierce, who studied this during his PhD. “That’s still the vision, but achieving it is incredibly complex.”
He believes home robots will become a reality someday—but not for at least another 10 to 15 years.